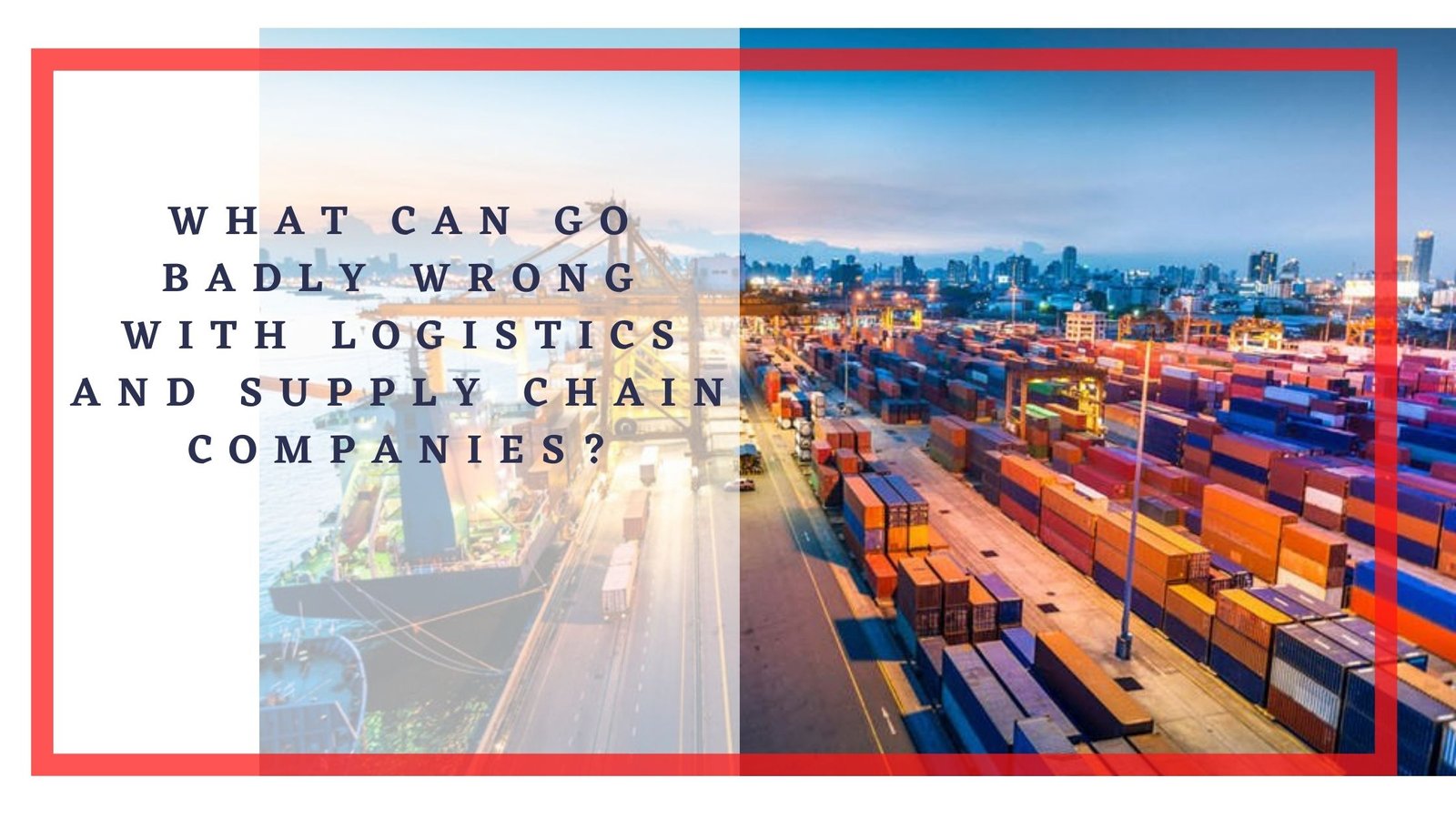
What can go badly wrong with logistics and supply chain companies?
We humans are not perfect, we make mistakes now and then and that’s not a matter of worry because it’s natural. No one is born perfect, we learn from our mistakes. While working in a team the work contribution from every individual is required to attain the final goal of the organization. A mistake made by a single person can affect the team’s performance, the ability of the management to reduce the losses as least as possible and bring work back to track defines its efficiency. Since logistics and supply, chain management is also teamwork, it requires maximum effort from every individual to attain the companies goal. Even the process of logistics and supply chain management can go wrong badly due to some human errors or external contingencies. Many times top logistics and supply chain companies in India have failed in their process, their ability to cause minimum loss defines their efficiency
The companies need to have a proper balance between supply and demand, they should adapt themselves to new technologies, their decisions made should be data and facts-driven. The top transport and logistics companies in India follow this funda thus creating a sustainable and competitive marketplace. The management should be strong and a good decision-maker, they should balance the capital and resources. Below are some of the areas on which the team has to continuously focus to avoid mistakes and losses to the company;
1. Process efficiency
Failure to focus on process efficiency is a common mistake done by small and medium-sized businesses because they still follow old conventional methods like use to paper-based work, not learning from industry practices, following processes that add no value to the customers, etc.
Since the market is highly competitive businesses should follow modern industry practices like the introduction of software, online payments, tracking, excellent customer response team, working and learning from mistakes, etc.
2. Transparency
Work on the process that you describe to the customers. Customers nowadays want a cost-effective movement of their goods along with tracking. If as a business you describe your process as hassle-free and secure you must update customers with every movement of their goods from pickup to delivery. No customer will be interested in logistics and supply chain services if the company doesn’t have an online tracking system.
3. Clear strategy
The company should have a clear strategy and the management should closely look upon it. Failure to follow the strategy can put the business at risk and unnecessary delay in the work process.
4. Inventory Management
Inventory management goes wrong not only with large companies, it goes wrong even with smaller businesses and startups. Too much inventory unnecessarily ties up too much cash. Errors in the data entry can impact the business process and planning due to errors in calculation. So to overcome this most of the companies opt for software-driven inventory management systems, such as barcode tracking and Radio Frequency Identification (RFID).
5. Supplier Relationships and Management
If this goes wrong can create a real problem for the business to a large extent. Suppliers should not be taken lightly and underestimated. The company should know the importance of building relationships with them. Working with a few or low suppliers can make the business shrink. The company should also constantly find and connect with the new suppliers for future supply.
6. Human Resource Investment
Humen resource investment refers to the investment in the employees of the company to educate them through employee training and skill developments. This process will replace the lost talented people in the company and will drive an efficient work process which will lead to more productivity. In the tough times when businesses are not up to the mark, the management may consider spending on educating their employees but they can choose certain energetic individuals for the training.